The accuracy and precision of tube laser cutting machines are essential in the production of high-quality parts. Quality Control (QC) is an important aspect of maintaining this accuracy and precision, as well as the overall performance of the machine. QC ensures that the machine performs to its fullest potential while also producing parts with exacting standards. This article will explore the role that QC plays in a tube laser cutting machine, and how it can help increase both safety and reliability.
Quality Control in Tube Laser Cutting
Pipe laser cutting machines are a staple of the manufacturing industry, and quality control is essential for ensuring maximum efficiency. Quality control in tube laser cutting safeguards the accuracy and repeatability of cuts, which is especially important when dealing with large quantities and complex designs. To ensure that high-quality products are produced without fail, operators must take a proactive approach to quality control by understanding the fundamentals of their laser cutter’s operation.
Functionality of a Tube Laser Cutting Machine
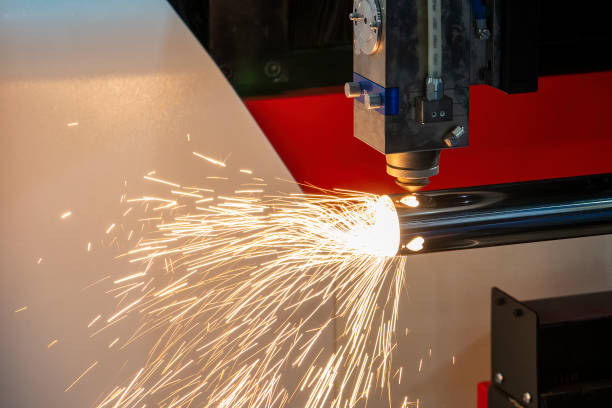
The functionality of such a machine depends heavily on the implementation of a strict quality control process in order to ensure that all items produced meet the highest standards of performance and safety. The most important component in this process is that each component must be inspected prior to being considered acceptable for use. This requires close attention to detail, as any flaws can potentially weaken the component or lead to failure down the road. In addition, proper operation and maintenance procedures must be followed rigorously in order to ensure optimal performance from the machine itself. All parts should also be regularly checked for signs of wear and tear, as well as any potential issues that may arise during use.
Steps for Doing Quality Control in Tube Laser Cutting Machine
Step 1: Preparing the Workpiece
Preparing the Workpiece is the most important part of doing quality control in tube laser cutting machines. It requires that all components are securely mounted and centered on the machine so that they will be cut precisely with minimal distortion. The workpiece must also be adequately clamped to the bed of the cutting machine to prevent it from moving or vibrating during cutting, which could lead to inaccurate cuts or even damage to the machine itself. Additionally, a clean surface free of debris is essential so that any dirt particles do not interfere with the beam’s path and potentially damage either component being cut or the machine itself. Finally, if a gas assist is used as part of your setup, it should be checked to ensure its pressurization levels are correctly set before feeding into your work area.
Step 2: Alignment & Focusing of Beam
Getting the right cut is essential in tube laser cutting machines. The second step in the process of quality control is alignment and focusing of beam. This step ensures that the laser beam is aligned correctly with the desired position on the material, and that it has been focused to create a precise cut. Alignment and focusing of beam can be done manually or automatically depending on what type of machine you are using. It involves adjusting the position, direction and focus of the laser beam to ensure accuracy when cutting through metal plates. Manual adjustment requires an operator to visually align the laser beam before turning it on, while automatic adjustment uses sensors and computers which can detect small variations in alignment more accurately than humans. It also helps reduce downtime for manual adjustments, resulting in higher productivity levels for businesses.
Step 3: Setting Up Process Parameters
Setting Up Process Parameters is an important step when doing quality control in tube laser cutting machines. It is essential to understand the parameters needed to produce the desired result and to set them up correctly. The parameters that need adjusting depend on the type of material being cut and what type of finish is desired. Generally, these include things such as speed, power, pulse frequency, and focal position; however, even these can vary depending on the specific machine model or material type used.
The operator should have a good understanding of how each parameter affects the final product in order to achieve optimal performance from the laser cutting machine. For instance, higher speeds may increase production rates but could also cause overheating if not adjusted properly. Conversely, too low a setting can cause damage due to insufficient power output for certain materials or applications.
Step 4: Monitor the Progress
This involves tracking production and making sure all operations are being carried out in accordance with required standards. Monitoring the progress of a tube laser cutting job helps to identify any potential issues that may arise during production, such as incorrect feed rate or improper tooling setup. It also allows for adjustments to be made quickly if needed, preventing wastage and improving overall productivity. With regular monitoring, manufacturers can reduce scrap rates and ensure high-quality products are consistently produced from their tube laser cutting machine.
Step 5: Post Processing Requirements
Operators must remove any dust or particles from the parts with an air blow gun or brush. This will help identify any areas of concern on the surface of the part, such as burrs and sharp edges. They should also visually inspect all parts for accuracy and conformity to drawings, specifications and tolerances.
Operators must measure surface roughness using a stylus profilometer in order to ensure it meets customer requirements. Finally, they should perform dimensional inspections such as radius checks and wall thickness measurements using calipers or other measuring tools.
Conclusion
The importance of quality control in any manufacturing process cannot be overstated, and a tube laser cutting machine is no exception. Quality control measures are necessary to ensure that the final product meets the customer’s expectations and requirements. A tube laser cutting machine can produce metal parts with high precision and accuracy, but if proper quality control procedures aren’t adopted, it could lead to costly defects or even accidents.
To ensure the best results from a tube laser cutting machine, quality control should start right at the beginning of production by regularly checking every step of the process—from selecting raw materials to installing components. To further guarantee safety and efficiency during operation, regular maintenance and inspections should also be done on a periodic basis. In addition, operators must be well-trained on how to use their equipment properly to prevent any errors from occurring in production.