Introduction
Laser cutting is a precise and efficient method of cutting materials such as steel, aluminum, and plastics. However, when laser cutting, slag can be a problem for many users. Slag is a by-product of the laser cutting process, and it can accumulate over time, making it difficult to achieve a smooth and precise cut. Fortunately, there are several strategies that can be used to reduce or eliminate the problem of laser cutting slag. In this article, we will discuss how to solve the problem of laser cutting slag, including the use of special cutting gases, advanced laser cutting systems, and careful maintenance of laser cutting equipment.
How to Minimize Slag When Laser Cutting: Techniques and Tips

First, it is important to use the correct settings for the material being cut. The laser cutting parameters should be adjusted to the thickness and type of material being cut, as well as the desired quality of the cut. For example, a slower cutting speed and a higher power setting are ideal for cutting thicker materials, as this increases the amount of heat at the point of contact and reduces the slag produced.
Second, it is important to select the right laser nozzle for the job. A larger nozzle is ideal for cutting thick materials, as it can disperse the heat more efficiently and reduce slag. However, a smaller nozzle is better suited for cutting thin materials, as it can cut with greater precision and accuracy.
Third, it is important to use a clean cutting surface. Dust and debris on the surface of the material can reduce the quality of the cut and increase slag. A clean, level surface should be used to ensure a precise cut.
Finally, when laser cutting, it is important to consider the environmental conditions. Hot and humid conditions can reduce the quality of the cut and increase slag. A well-ventilated space should be used to ensure the laser cutting process is not affected by the environment.
Using Anti-Splatter Agents to Reduce Slag During Laser Cutting
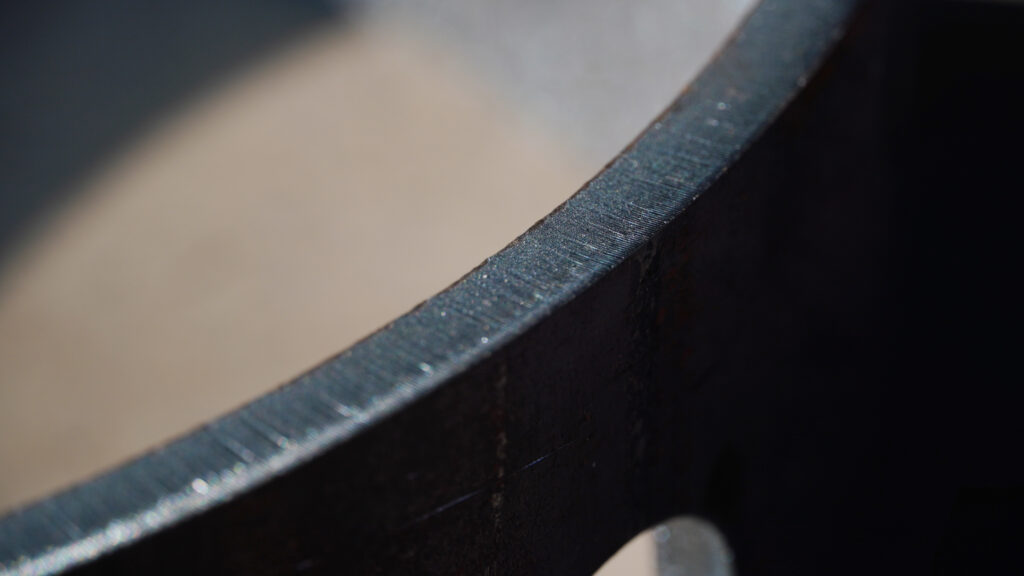
Laser cutting is a highly accurate and efficient method of cutting metals and other materials. However, it can sometimes produce slag, which is a by-product of material that has been heated and vaporized during the cutting process. Slag can reduce the quality of the cut, interfere with the cutting process, and reduce the overall efficiency of the laser cutting process. To reduce the amount of slag produced during laser cutting, anti-splatter agents can be used.
Anti-splatter agents are additives that are applied to the material before the laser cutting process begins. These agents work to reduce the amount of slag produced by preventing the molten material from sticking to the cutting surface. They also reduce the amount of heat generated from the laser cutting process, which reduces the likelihood of slag formation.
When using anti-splatter agents, it is important to select the correct agent for the material being cut. Different materials require different agents, so it is important to read the product labels and select the correct one for the job. It is also important to apply the agent correctly, as too much or too little can have an adverse effect on the cutting process.
Anti-splatter agents can be applied to the material in a variety of ways, depending on the specific agent being used. Some agents are applied by spraying, while others are applied with a brush or roller. For best results, it is important to follow the manufacturer’s instructions when using any anti-splatter agent.
Using anti-splatter agents can significantly reduce the amount of slag produced during laser cutting processes. This can help to improve the quality of the cut and the efficiency of the process. It is important to select the correct agent and apply it correctly to ensure maximum effectiveness.
Exploring the Benefits of Automated Slag Removal for Laser Cutting
One significant benefit of automated slag removal is the improved quality of cuts. Automated slag removal systems can ensure that each cut is clean, with no residual slag left behind. This eliminates the need for additional manual slag removal, which can be time consuming and labor intensive. Additionally, automated slag removal eliminates the possibility of human error, resulting in a consistent level of cut quality for every job.
Automated slag removal can also significantly improve the speed of laser cutting operations. By eliminating the need for manual slag removal, automated slag removal systems can drastically reduce the amount of time required to complete a job. This can allow laser cutters to take on more jobs, increase their production rate, and ultimately boost their profits.
Finally, automated slag removal can also increase the efficiency of laser cutting operations. Automated slag removal systems are designed to be highly efficient, significantly reducing the amount of energy required to complete a job. This can help to reduce energy costs associated with laser cutting operations, leading to increased profits.
Troubleshooting Common Problems with Laser Cutting Slag
Working with laser cutting machines can be a great way to produce parts and components with a high level of precision. However, from time to time, issues can arise with the cutting process, such as the presence of slag. Slag is a byproduct of the laser cutting process, and if it is not dealt with properly, it can lead to a range of quality issues. In this article, we will look at some of the common problems associated with slag and how they can be addressed.
The first issue is that the slag can cause a rough finish on the edges of the cut material. This is due to the high temperature of the laser, which can cause the metal to melt and form small droplets which then solidify on the edge of the cut. To reduce this, it is important to make sure that the laser is set to the correct power level and that the cutting speed is not too high. This will help to reduce the amount of heat generated and the amount of slag produced.
The second issue is that the slag can lead to porosity in the cut material. This is due to the molten droplets that form on the cutting edge, which can become trapped in the material as it cools. To reduce the risk of porosity, it is important that the laser is set to the correct power level and that the cutting speed is not too high. It is also important to make sure that the edge of the material is kept clean and free of any debris.
Finally, the presence of slag can cause a build-up of heat in the cutting area. This can lead to distortion of the material and can also cause a poor cut quality. To reduce the risk of heat build-up, it is important to ensure that the cutting area is adequately ventilated and that the laser is set to the correct power level.
What You Need to Know About Laser Cutting Slag Removal
Laser cutting is a process used to cut through materials like metal, plastic, and wood with the use of a laser. The laser is used to heat and melt the material so that it can be cut into desired shapes and sizes. Laser cutting can provide a clean, precise cut with minimal distortion, making it a popular choice for industrial and manufacturing applications.
One of the challenges with laser cutting is the build-up of slag. Slag is a byproduct created when the laser beam melts the material. It is a molten mixture of molten material mixed with molten metal and other impurities. This slag is then deposited onto the cutting surface, leading to rough edges and an uneven cut.
To prevent slag buildup, it is important to use the right cutting parameters. These parameters depend on the material being cut and the laser used. A low cutting speed and a high power setting are typically used. It is also important to use the right nozzle diameter and to keep the nozzle clean.
In addition to using the right parameters, it is also important to use the right cutting gases. These gases help to reduce the amount of slag that is created by creating a protective atmosphere around the cutting area. The most commonly used cutting gases are oxygen and nitrogen.
Once the cut is complete, it is important to remove the slag from the material. This can be done by using a slag remover. A slag remover is a specialized tool that is used to physically remove the slag from the material. It works by using a vacuum to remove the slag from the material.
Optimizing the Laser Power Settings for Slag Reduction in Laser Cutting
Laser cutting is a versatile and reliable technology used in a variety of industries for cutting and engraving a range of materials. While laser cutting offers many advantages, such as high accuracy and repeatability, one of the main challenges is the production of slag, or molten material, which is created during the cutting process. This slag can have a negative impact on the quality of the finished product, as well as the cutting speed and efficiency.
The amount of slag produced during laser cutting is determined by a range of factors, including the laser power settings used. Optimizing the laser power settings is an important step in reducing the amount of slag produced. This means adjusting the power settings to the lowest level possible while still achieving the desired cut quality.
The first step in optimizing the laser power settings is to identify the correct settings for the material being cut. This will depend on the type of material and thickness, as well as the desired cut quality. If the material is too thick, the laser power settings may need to be increased in order to achieve the desired cut quality.
Once the correct settings have been identified, the next step is to adjust the laser power settings to the lowest level possible while still achieving the desired cut quality. This can be done by adjusting the pulse frequency and pulse width of the laser. Pulse frequency is the number of times the laser pulses per second, and pulse width is the length of time the laser pulses. By reducing the pulse frequency and pulse width, the laser power can be reduced while still achieving the desired cut quality.
Finally, the laser power settings should be tested and adjusted if necessary. This can be done by running test cuts on scrap material and adjusting the laser power settings until the desired cut quality is achieved with the lowest possible laser power.
Conclusion
The problem of laser cutting slag can be solved by proper maintenance of the laser cutting machine, proper selection of cutting parameters, and regular monitoring of the cutting process. By following these steps, the amount of slag produced can be significantly reduced, thus increasing the efficiency of the laser cutting process. Additionally, the use of laser cutting slag removal tools, such as a slag remover, can help to further reduce the amount of slag produced during the laser cutting process.