The need for efficiency and cost savings has become increasingly important in the manufacturing industry. As a result, many metal fabrication processes have been revolutionized with the introduction of tube laser cutting machines. This article will explore how utilizing this technology can help maximize material efficiency while achieving precision results with minimal waste. We’ll look at why tube laser cutting machines are an ideal solution for metal fabrication projects and discuss the potential cost savings that come with implementing this technology.
Benefits of Tube Laser Cutting
Tube laser cutting offers many advantages compared to traditional methods of cutting tubes. It can create intricate designs with fewer steps, reducing production time significantly. Additionally, it eliminates the need for secondary operations such as grinding or deburring which allows for faster turnaround times as well as less waste material generated during production. With tube laser cutting, manufacturers can save time and money by maximizing material efficiency while still achieving exact results every time.
Advantages of a Tube Laser Cutting Machine
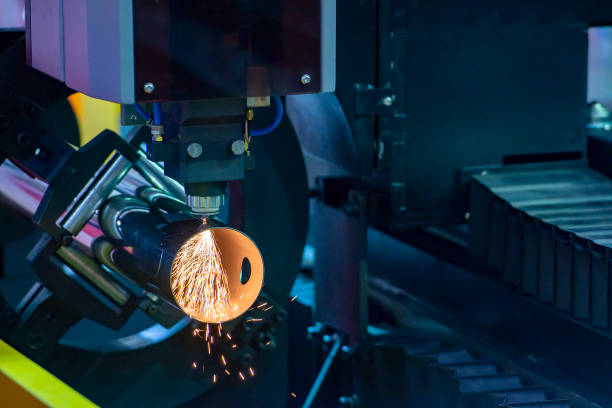
A tube laser cutting machine can increase productivity by providing quick and accurate results with its sophisticated automation technology. This type of equipment is capable of producing complex parts in a fraction of the time it would take using traditional methods such as saws or drills. Additionally, the technology used in this type of machine allows for more intricate cuts that are impossible with other types of machinery. The increased accuracy also assists in reducing material wastage and increasing cost savings during fabrication processes.
How to Maximize Material Efficiency
Maximizing material efficiency is an important goal for any company in the metal fabrication industry. With the right equipment and processes in place, a business can drastically reduce waste and increase their profits. A tube laser cutting machine is one of the most efficient ways to maximize material efficiency while ensuring quality cuts and quick turnaround times.
The tube laser cutting machine offers precision cuts that create minimal scrap, meaning that businesses don’t have to throw away as much excess material during each project. This increased accuracy also allows companies to use thinner materials than before, further reducing their costs. Additionally, with faster processing speeds than other available methods, businesses can reduce labor costs by completing projects more quickly – allowing them to take on more jobs with less overhead.
Setting Up the Tube Laser Cutter
Tube laser cutting machines are a great addition to any fabrication or manufacturing business. By combining the power of a laser with the convenience of a computer-controlled system, businesses have the ability to quickly and accurately cut tubes into almost any shape. Setting up this machine can be daunting at first, but it’s essential to maximize its efficiency when cutting materials like aluminum, steel, brass, and more.
The setup process involves calibrating the machine for optimal accuracy based on the material being cut. This includes adjusting power levels, speed controls, and focusing lenses for precise results every time. Additionally, operators must ensure that all safety protocols are followed during setup such as wearing protective gear and keeping work areas clean. After installation is complete and all safety precautions are in place, operators can begin using the tube laser cutter to produce high-quality parts in no time!
Automation for Improved Efficiency
Automation is revolutionizing the industrial sector, allowing for improved efficiency and productivity. With a tube laser cutting machine, companies can maximize their material efficiency with the help of automated processes. The machine combines computer-aided design (CAD) drawings with high-powered laser beams to automatically cut metal parts into specific shapes and sizes. This enables more efficient production processes and ensures accuracy in cuts, resulting in reduced material wastage and cost savings. Furthermore, this advanced machinery can perform multiple tasks without manual intervention while reducing the complexity of traditional cutting methods. By leveraging automation technology, companies can produce quality products faster than ever before while optimizing their use of resources. With a tube laser cutting machine at its disposal, businesses can effectively improve their operational efficiency levels and bring down manufacturing costs too.
Considerations for Material Usage
The type of material being used is important. Aluminum, stainless steel, and carbon steel are some of the most commonly used materials for tube laser cutting machines since they offer good thermal conductivity and are relatively easy to form. Additionally, thickness and size should be taken into account when selecting materials. Thin metal sheets require less energy to cut than thicker ones while larger pieces require more strength from the machine. It is also important to consider what kind of components will be manufactured using the tube laser cutting machine. Certain components may need extra steps or certain materials that can affect the overall efficiency of the process. For example, if parts require welding or bending after they have been cut, then heavier gauge metals may be needed for increased strength during these processes.
Conclusion: Benefits of Optimizing Efficiency
Optimizing efficiency is a surefire way to increase the productivity of any business. With the introduction of tube laser cutting machines, material efficiency can be maximized with ease. The benefits of optimizing efficiency are numerous and can help businesses save money and time in their production processes.
Tube laser cutting machines offer increased precision, accuracy and speed when compared to traditional cutting methods. This allows companies to produce goods faster without compromising on quality or spending extra money. Additionally, these machines require less energy consumption compared to traditional methods which reduces operational costs significantly. Furthermore, they generate minimal waste which helps reduce environmental impact while saving on labour costs as fewer people are needed to set up and operate the machinery.
In conclusion, optimizing efficiency with a tube laser cutting machine has many advantages that make it an attractive option for businesses across industries looking for cost savings and increased productivity levels.