Introduction:
Laser cutting has many advantages over traditional cutting methods. It is faster, more accurate, and produces less waste. Laser cutting can also be used on delicate materials that would be damaged by other cutting methods. Welding is a process that joins two pieces of metal together by melting and fusing them. laser welding is a type of welding that uses a laser to create the weld. Laser welding is faster and more accurate than traditional welding methods, and it produces less waste.
What is laser cutting and how does it work?
Laser cutting is a technology that uses a laser to cut materials, and it can be used for a variety of purposes. Laser cutting has many advantages over other methods of cutting, such as being more precise, having a cleaner cut, and being faster. It works by using a focused beam of light to heat up the material until it reaches its melting point. The laser then vaporizes the material, making a clean cut. Laser cutting is an extremely versatile technology that can be used for a variety of applications. Some examples include cutting sheet metal, fabric, wood, and plastics.
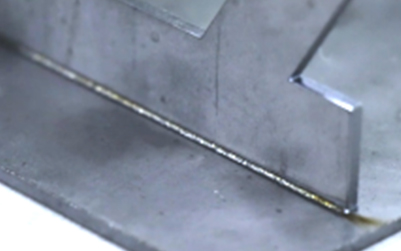
The advantages of laser cutting on welded joint production
As the world of manufacturing and production continues to evolve, so too do the methods and machines used to create the products we use every day. In recent years, laser cutting has become an increasingly popular method for creating welded joints in various materials. This is due to the many advantages that laser cutting offers over traditional methods, such as plasma cutting or waterjet cutting. Laser welding allows welds to be made with a high aspect ratio (large depth to narrow width). Laser welding, therefore, is feasible for joint configurations that are unsuitable for many other (conduction-limited) welding techniques, such as stake welding through lap joints. Additionally, laser welding can minimize the heat-affected zone, thus reducing the potential for distortion.
Some of the advantages of using laser cutting to create welded joints include:
1. Increased accuracy: Laser cutting offers a much higher degree of accuracy than other methods, which is essential when creating welded joints.
2. Increased speed: Laser cutting is a much faster method than other methods of cutting, which can save time and money in the production process.
3. Reduced heat: Because laser cutting uses a beam of light to cut materials, there is less heat involved in the process. This can be beneficial when working with heat-sensitive materials.
4. Reduced noise: Laser cutting is a much quieter process than other methods, which can be beneficial in a manufacturing setting.
5. Increased versatility: Laser cutting can be used to cut a variety of different materials, including metals, plastics, and wood.
The benefits of using laser cutting in welding
One of the benefits of using laser cutting in welding is that it can help to improve the accuracy of welds. This is because the laser beam can be focused very precisely on the area that needs to be welded, meaning that there is less chance of error.
Another benefit of using laser cutting in welding is that it can help to improve the speed of welds. This is because the laser beam can travel much faster than traditional methods, such as arc welding. This means that less time is needed to complete a weld, which can be particularly beneficial in industries where time is often of the essence.
Product recommended:
The advantages of laser cutting over other methods
Another method of laser welding is the hybrid laser-arc welding process. Combining arc welding and deep penetration laser welding simultaneously in the same weld pool, this method of laser welding combines the individual advantages of both arc welding and laser processes.
Laser cutting is a technology that has been around for quite some time, but has only recently been used in welding. This process uses a high-powered laser to cut through metal, and can be used on both ferrous and non-ferrous metals.
As more and more organizations look for ways to improve their production processes, many are turning to laser cutting as a way to increase efficiency and reduce costs. One of the key advantages of laser cutting is the fact that it can be used to create welded joints that are stronger and more precise than those created using traditional methods.
Welded joints created using laser cutting are not only stronger, but they are also less likely to experience corrosion and can be created with a much higher degree of precision. This is due to the fact that laser cutting produces a cleaner cut than traditional methods, meaning that there is less of a chance for the material to be damaged during the welding process.
Another advantage of laser cutting is that it is a much faster process than traditional methods, meaning that organizations can increase their production rate without sacrificing quality. This is particularly beneficial for those organizations that require a high volume of welded joints on a regular basis.
Conclusion:
Overall, laser cutting is a highly versatile and precise method of welded joint creation that offers a range of benefits for organizations of all sizes. Whether you require a high volume of welded joints or simply want to improve the quality of your existing production processes, laser cutting is definitely worth considering.