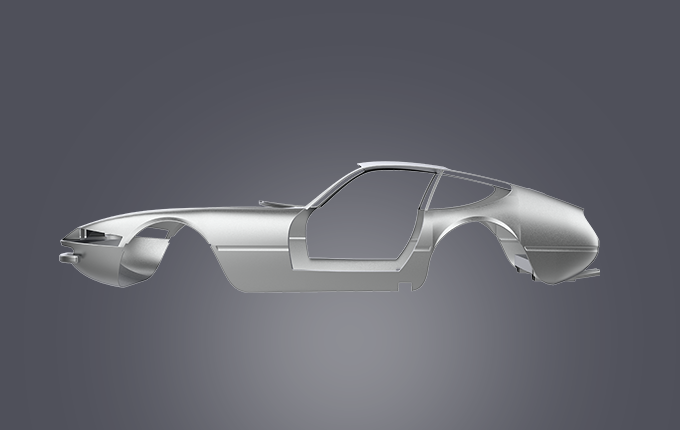
The manufacturing industry has had a long and illustrious history of utilizing cutting-edge technology to increase efficiency and produce quality products. One such example is the tube laser cutting machine, which has revolutionized the way manufacturers go about producing parts for a variety of projects. By using this computer-controlled machine, manufacturers can quickly and accurately cut intricate shapes out of metal tubes and pipes with unparalleled precision.
Tube Laser Cutting
Tube laser cutting is an essential technology for many industries, allowing manufacturers to cut complex shapes with high precision and accuracy. This process utilizes a powerful laser beam that is transmitted through a series of mirrors and lenses to create precise cuts in materials such as stainless steel, aluminum, copper and brass. With tube laser cutting, manufacturers can produce parts with intricate details or tight tolerances in less time and with greater cost efficiency than traditional methods such as machining or grinding.
The use of tube laser cutting machines offers numerous benefits compared to other manufacturing processes. It eliminates the need for tooling, which significantly reduces costs associated with production runs. Additionally, it produces minimal waste material and no heat affected zones (HAZ) due to the non-contact nature of the process. This makes it suitable for producing small parts without damage from heat build-up or distortion from pressure applied by traditional cutting methods.
Benefits of Tube Laser Cutting
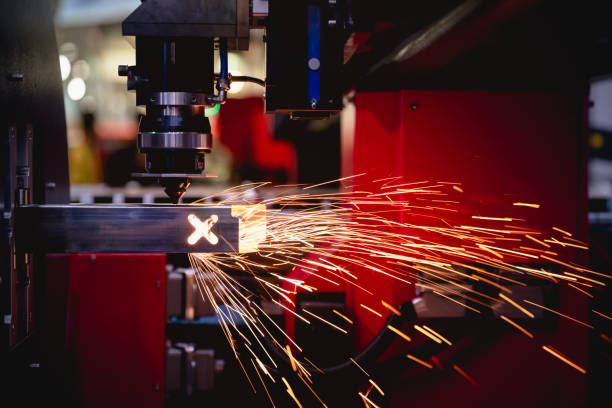
Tube laser cutting machines have revolutionized the manufacturing industry. Using a tube laser cutting machine, manufacturers can quickly and accurately cut tubular materials into components for use in a variety of applications. These machines are both time-saving and cost-effective, providing many benefits to industrial production processes. The main benefit of a tube laser cutting machine is its ability to provide precise cuts with high accuracy and repeatability. This means that the same product will be created every time, reducing costs associated with waste or rework from incorrect cuts. Additionally, tubes can be cut with no secondary processing required, saving both time and money on labour costs as well as increasing productivity levels. Furthermore, these machines are able to produce intricate parts in various shapes with smooth finishes that meet any application requirements without the need for costly tooling changes between jobs.
Applications in Manufacturing
The manufacturing industry is ever-evolving, with advanced technologies and applications being introduced to make the process more efficient. One of the most popular tools used in modern manufacturing is a tube laser cutting machine. This technology has revolutionized the way manufacturers approach their production processes. Tube laser cutting machines are computer controlled systems used to cut metal tubes into predetermined shapes and sizes. They use high powered lasers to heat and melt materials such as steel, aluminum, brass, and copper at incredibly precise temperatures. Not only do they provide greater accuracy than conventional cutting methods, but they also reduce production times significantly. As such, these machines are becoming an increasingly important tool for manufacturers in various industries that rely on precision cutting services like automotive parts fabrication or medical equipment production.
Advantages over Other CNC Technologies
The role of a tube laser cutting machine in manufacturing is becoming increasingly important as new technologies emerge. This type of cutting machine offers reliable performance and enhanced flexibility when compared to other CNC technologies. Tube laser cutting machines have several advantages that make them ideal for many industrial applications. One advantage is their ability to rapidly cut through materials such as steel, aluminum, copper, brass and titanium with incredible precision. The beam generated by the laser enables these machines to produce clean cuts at high speeds without leaving any burrs or rough edges along the cut edge. This helps reduce production time and costs since there is no need for additional finishing processes such as grinding or sanding after the cutting process is complete. Tube laser cutting machines also offer greater flexibility than traditional CNC milling machines due to their capability of handling more complex shapes and designs quickly and accurately.
Challenges with Tube Laser Cutting
Tube laser cutting is a fast and efficient process used in manufacturing to create intricate parts from metal tubes. However, it is not without its challenges. One of the main challenges with tube laser cutting is that the precision of the cuts can be difficult to achieve. Due to the complexity of using a laser, it requires an experienced operator who understands how to make adjustments and calibrations for optimal performance. In addition, there are certain vibration issues associated with tube laser cutting that can also lead to inaccuracies in cut quality. This means that frequent maintenance must be done on the machine in order to reduce these problems and ensure consistent results. Another challenge with tube laser cutting is managing thermal distortions caused by heat generated during the process. To combat this issue, some manufacturers provide special coolants or gas mixtures that help maintain temperature control while also protecting components from damage due to excessive heat exposure.
Companies Adopting Tube Laser Cutting Machines
As companies look to become more efficient and cost effective, the integration of tube laser cutting machines can be a key factor in achieving success. This technology is quickly becoming the standard for many industries and has revolutionized the way businesses operate. The use of tube laser cutting machines allows businesses to produce products with higher accuracy and precision than ever before. With this machinery, manufacturers can cut intricate shapes, smooth edges and create unique designs with ease. Additionally, they can significantly reduce material waste while increasing production speeds which leads to lower overhead costs and higher profits. These advancements have made tube laser cutting machines one of the most sought-after pieces of equipment in the modern industry today. Companies across all sectors are taking advantage of this technology to further improve their competitiveness in an ever-changing market landscape.
Conclusion
Tube laser cutting machines offer an efficient and accurate method for cutting metal tubes and pipes. As these machines increase in popularity, manufacturers should consider investing in one to improve their production process, reduce costs, and boost production quality. Tube laser cutting machines are a worthwhile investment due to the many benefits they offer to manufacturers. They can easily cut materials like aluminum, stainless steel, copper alloys, brass and titanium with high accuracy as well as precision. Additionally, tube laser cutting machines also help reduce material waste by accurately controlling the size of each cut piece. Furthermore, this machine does not require additional fixtures or tooling which further decreases cost associated with manufacturing.